PE water supply pipe welding steps
PE water supply pipe welding steps
PE material is used in the manufacturing of water supply pipes due to its high strength, corrosion resistance, non-toxicity and other characteristics. Because it does not rust, it is an ideal pipe material to replace ordinary iron water supply pipes. Next, the editor of Desu will give you a detailed explanation of the welding steps of PE water supply pipes, so that you can get started better when installing PE water supply pipes.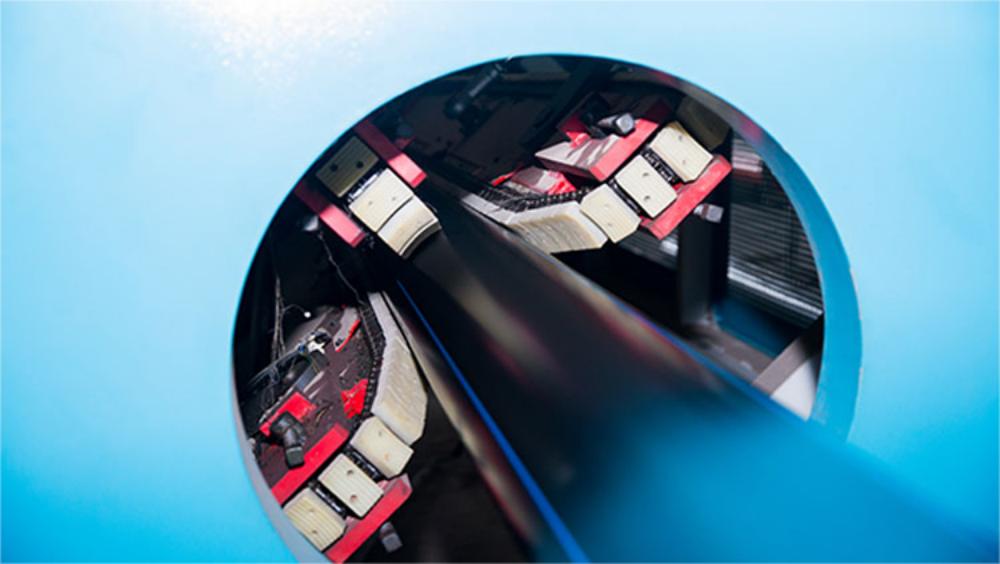
Desu PE drainage pipe editor explains in detail the welding steps of PE water supply pipes:
PE water supply pipe is made of special polyethylene as raw material and extruded by a plastic extruder in one go. It is used in urban water supply pipe networks, irrigation water diversion projects and agricultural sprinkler irrigation projects. It is especially suitable for plastic pipes that are resistant to acid, alkali and corrosion environments. Because PE pipes are connected by hot melt or electric heat melt, which realizes the integration of the interface and the pipe, and can effectively resist the hoop stress and axial impact stress generated by the pressure. Moreover, the PE pipe does not add heavy metal salt stabilizers, and the material is non-toxic. , does not scale, does not breed bacteria, and avoids secondary pollution of drinking water. The welding of PE water supply pipes can be divided into the following steps, which are very important. Everyone must pay attention to them.
(1) When welding PE water supply pipes, align the axes of the two pipes and fix the ends of the two pipes by spot welding.
(2) When welding the PE water supply pipe to the flange, the water supply pipe should be inserted into the flange first. After spot welding, use a square to align it. Level it before welding. The flange should be welded on both sides, and the inside of the flange should not be welded beyond the flange. Closed surface.
(3) When the wall thickness of the PE water supply pipe is more than 5mm, the bevel should be cut to ensure full penetration. The bevel can be formed by gas welding cutting or bevel machining, but the slag and iron oxide should be removed and polished with a file until reveal metallic light
(4) When cutting steel pipes, the cutting surface should be perpendicular to the center line of the pipe to ensure the concentricity of the pipe after welding.
(5) The flange should be perpendicular to the center line of the pipe, and the surfaces should be parallel to each other. The flange gasket must not protrude into the pipe. The specifications of the bolts connecting the flange should match the flange. The length of the protruding nut of the screw should not be greater than 1/1 of the diameter of the screw. 2.
(6) When welding water supply pipes, the pipe interfaces must be cleaned of floating rust, dirt and grease.
(7) The flange gasket should be selected according to the drawings and specifications. The cold water system uses a rubber gasket, and the hot water system uses an asbestos rubber gasket.
PREVIOUS:DESU PE pipe connection method
No next